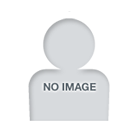
YOKOUCHI YASUTO
Emeritus Professor etc. | Emeritus Professor |
Researcher Information
Field Of Study
Educational Background
- 1971
The University of Tokyo, 工学系研究科, 機械工学専攻, Japan - 1971
The University of Tokyo, Graduate School, Division of Engineering - 1968
The University of Tokyo, 工学系研究科, 機械工学専攻, Japan - 1968
The University of Tokyo, Graduate School, Division of Engineering - 1965
The University of Electro-Communications, Faculty of Electro-Communications, 通信機械工学科, Japan - 1965
The University of Electro-Communications, Faculty of Electro Communications
Research Activity Information
MISC
- Rigid-plastic hybrid element analyses of the plane strain upsetting
YM Guo; K Nakanishi; Y Yokouchi
A rigid-plastic hybrid element method (HEM) for simulation of metal forming is developed. This method is a mixed approach of the rigid-plastic domain-BEM and the rigid-plastic FEM based on the theory of compressible plasticity. Because the compatibilities of not only velocity but also velocity's derivative between the adjoining boundary elements and finite elements can be met, the velocities and the derivatives of the velocity can be calculated with the same precision for the rigid-plastic HEM. Then, it is considered that the rigid-plastic HEM is a more precise method in formulation than the conventional rigid-plastic FEMs for which the compatibilities of velocity's derivative cannot be met. The plane strain upsetting processes with two friction factors are analyzed by the rigid-plastic HEM in this article. (C) 2002 Wiley Periodicals, Inc., JOHN WILEY & SONS INC, Nov. 2002, NUMERICAL METHODS FOR PARTIAL DIFFERENTIAL EQUATIONS, 18, 6, 726-737, English, 0749-159X, WOS:000178794200003 - Rigid-plastic hybrid element analyses of the plane strain upsetting
YM Guo; K Nakanishi; Y Yokouchi
A rigid-plastic hybrid element method (HEM) for simulation of metal forming is developed. This method is a mixed approach of the rigid-plastic domain-BEM and the rigid-plastic FEM based on the theory of compressible plasticity. Because the compatibilities of not only velocity but also velocity's derivative between the adjoining boundary elements and finite elements can be met, the velocities and the derivatives of the velocity can be calculated with the same precision for the rigid-plastic HEM. Then, it is considered that the rigid-plastic HEM is a more precise method in formulation than the conventional rigid-plastic FEMs for which the compatibilities of velocity's derivative cannot be met. The plane strain upsetting processes with two friction factors are analyzed by the rigid-plastic HEM in this article. (C) 2002 Wiley Periodicals, Inc., JOHN WILEY & SONS INC, Nov. 2002, NUMERICAL METHODS FOR PARTIAL DIFFERENTIAL EQUATIONS, 18, 6, 726-737, English, 0749-159X, WOS:000178794200003 - アダプティブメッシュ法に基づく可変節点数要素の弾塑性有限要素解析への適用
Sep. 2002, 理研シンポジウムものつくり情報技術統合化研究(第2回), 71-76 - 可変節点数要素の弾塑性有限要素解析への適用(第2報)
May 2002, 平成14年度塑性加工春季講演会講演論文集, 143-144 - 可変節点数要素の弾塑性有限要素解析への適用
Oct. 2001, 第52回塑性加工 連合講演会講演論文集, 235-236 - フランジしわのFEM解析
Jul. 2001, 日本塑性加工学会塑性力学分科会,板材のし わ・スプリングバック問題における塑性力学的アプロ-チ資料集, 1-8 - Five-node Shell Element for Transition Region from a Fine to a Coarse Mesh, Simulation of Materials Processing; Theory, Methods and Applications (Ed. K. Mori)
Jun. 2001, Proc. 7th Int. Conferemce on Numerical Methods in Industrial Forming Process -- NUMIFORM 2001, Toyohashi, Japan, Balkema Publishers, 645-650 - Five-node Shell Element for Transition Region from a Fine to a Coarse Mesh, Simulation of Materials Processing; Theory, Methods and Applications (Ed. K. Mori)
Jun. 2001, Proc. 7th Int. Conferemce on Numerical Methods in Industrial Forming Process -- NUMIFORM 2001, Toyohashi, Japan, Balkema Publishers, 645-650 - ソリッド縮退シェル要素を用いた有限要素解析における粗密分割 の継目の考察
May 2001, 日本計算工学会論文集,日本計算工学会, 3, 271-276 - 有限要素解析における粗密分割の継目のための5節点シェル要素
Nov. 2000, 第51回塑性加工連合講演会講演論文集, 195-196 - 分岐の考慮の有無によるFE解析結果のちがい
Nov. 2000, 第51回塑性加工連合講演会講演論文集, 193-194 - 薄板変形解析における要素分割様式による結果の比較
Nov. 2000, 第51回塑性加工連合講演会講演論文集, 191-192 - 粗密分割の継目のための5節点シェル要素
Sep. 2000, 非線形解析プログラム研究会精度向上分科会, 1-2 - Hot backward extrusion comparative analyses by a combined finite element method
YM Guo; Y Yokouchi; K Nakanishi
Deformation and temperature of hot backward extrusion are complex owing to interaction between deformation and temperature. In this paper, two- and one-way axisymmetric hot backward extrusion problems are analyzed by a combined finite element method, which consists of the volumetrically elastic and deviatorically rigid-plastic finite element method and the heat transfer finite element method. The volumetrically elastic and deviatorically rigid-plastic finite element method is different from the conventional rigid-plastic finite element methods, and has some merits in comparison with the conventional methods. Because contact surfaces between workpiece and tools of the one-way extrusion are different from those of the two-way one, the deformation and temperature of the one-way extrusion are different from those of the two-way one. Contours of effective strain rate, effective strain, temperature, effective stress and hydrostatic stress, as well as plots at different reductions for the two extrusions are obtained successfully. Differences of calculated results for the two extrusions can be clearly seen through comparative analyses.
Because the bulk modulus is introduced into the volumetrically elastic and deviatorically rigid-plastic finite element method, influence of temperature on hydrostatic stress can be considered in this paper. (C) 2000 Elsevier Science Ltd. All rights reserved., PERGAMON-ELSEVIER SCIENCE LTD, Sep. 2000, INTERNATIONAL JOURNAL OF MECHANICAL SCIENCES, 42, 9, 1867-1885, English, 0020-7403, WOS:000087795800010 - Hot backward extrusion comparative analyses by a combined finite element method
YM Guo; Y Yokouchi; K Nakanishi
Deformation and temperature of hot backward extrusion are complex owing to interaction between deformation and temperature. In this paper, two- and one-way axisymmetric hot backward extrusion problems are analyzed by a combined finite element method, which consists of the volumetrically elastic and deviatorically rigid-plastic finite element method and the heat transfer finite element method. The volumetrically elastic and deviatorically rigid-plastic finite element method is different from the conventional rigid-plastic finite element methods, and has some merits in comparison with the conventional methods. Because contact surfaces between workpiece and tools of the one-way extrusion are different from those of the two-way one, the deformation and temperature of the one-way extrusion are different from those of the two-way one. Contours of effective strain rate, effective strain, temperature, effective stress and hydrostatic stress, as well as plots at different reductions for the two extrusions are obtained successfully. Differences of calculated results for the two extrusions can be clearly seen through comparative analyses.
Because the bulk modulus is introduced into the volumetrically elastic and deviatorically rigid-plastic finite element method, influence of temperature on hydrostatic stress can be considered in this paper. (C) 2000 Elsevier Science Ltd. All rights reserved., PERGAMON-ELSEVIER SCIENCE LTD, Sep. 2000, INTERNATIONAL JOURNAL OF MECHANICAL SCIENCES, 42, 9, 1867-1885, English, 0020-7403, WOS:000087795800010 - 体積弾性・偏差剛塑性有限要素法による熱間鍛造の比較解析
May 2000, 平成12年度塑性加工春季講演会講演論文集, 59-60 - 薄鋼板における二次分岐変形の解析
May 2000, 平成12年度塑性加工春季講演会講演論文集, 27-28 - 有限要素解析における粗密分割領域の継目の考察
Apr. 2000, 塑性と加工, 41, 471, 395-399 - ヒンジ-コニカル要素を用いた軸対称殻の弾塑性解析
Feb. 2000, 塑性と加工, 41, 469, 156-160 - 面内2軸荷重を受ける薄板の分岐解析
Oct. 1999, 第50回塑性加工連合講演会講演論文集, 195-196 - 選択低減積分を施した可変節点数要素の塑性加工問題への適用
Oct. 1999, 第50回塑性加工連合講演会講演論文集, 131-132 - Hot forging simulation by the volumetrically elastic and deviatorically rigid-plastic finite-element method
Y. M. Guo; K. Nakanishi; Y. Yokouchi
The authors have formulated the volumetrically elastic and deviatorically rigid-plastic finite-element method and have verified that this method has some merits such as automatic error-correcting by comparison with conventional rigid-plastic finite element methods. In this paper, an axisymmetric hot forging of 1015 steel is analyzed by the volumetrically elastic and deviatorically rigid-plastic finite element method. The forging processes of from 0 to 30% reduction in the vertical height of the dies are simulated. To consider the thermal effect of the hot forging, a combined simulation of plastic deformation and heat transfer with finite element methods is done. The numerical results are visualized by post-processing. Contours of temperature, effective strain rate, effective strain, effective stress, volume strain rate, hydrostatic stress and shear stress, as well as nodal velocity fields are obtained successfully., Elsevier Science S.A., 19 May 1999, Journal of Materials Processing Technology, 89-90, 111-116, English, 0924-0136, 80011112785, 0345533944 - Hot forging simulation by the volumetrically elastic and deviatorically rigid-plastic finite-element method
Y. M. Guo; K. Nakanishi; Y. Yokouchi
The authors have formulated the volumetrically elastic and deviatorically rigid-plastic finite-element method and have verified that this method has some merits such as automatic error-correcting by comparison with conventional rigid-plastic finite element methods. In this paper, an axisymmetric hot forging of 1015 steel is analyzed by the volumetrically elastic and deviatorically rigid-plastic finite element method. The forging processes of from 0 to 30% reduction in the vertical height of the dies are simulated. To consider the thermal effect of the hot forging, a combined simulation of plastic deformation and heat transfer with finite element methods is done. The numerical results are visualized by post-processing. Contours of temperature, effective strain rate, effective strain, effective stress, volume strain rate, hydrostatic stress and shear stress, as well as nodal velocity fields are obtained successfully., Elsevier Science S.A., 19 May 1999, Journal of Materials Processing Technology, 89-90, 111-116, English, 0924-0136, 80011112785, 0345533944 - 静的陰解法について
Jan. 1999, 第4回板成形シミュレーション利用技術研究会, 1-14 - A comparison between the volumetrically elastic and deviatorically rigid-plastic FEM and the penalty rigid-plastic FEM
YM Guo; Y Yokouchi; K Nakanishi; S Kamitani
The volumetrically elastic and deviatorically rigid-plastic finite element method (FEM) is a different method from the conventional penalty rigid-plastic FEM, and has some merits in comparison with the penalty rigid-plastic FEM. To secure numerical evidence on the difference between the two kinds of methods and to show the merits of the volumetrically elastic and deviatorically rigid-plastic FEM, this paper makes analyses of the upsetting of an aluminium alloy column by the two kinds of methods. Then, normal solutions are compared with deviant solutions that are given by relaxing convergence criteria of the iterative solution in a calculated step by the two kinds of methods, respectively. In this way, it can be clarified that the errors of the step virtually disappear, and that the calculated results are largely corrected in the next step and the later steps for the volumetrically elastic and deviatorically rigid-plastic finite element analysis. Copyright (C) 1999 John Wiley & Sons, Ltd., JOHN WILEY & SONS LTD, Jan. 1999, COMMUNICATIONS IN NUMERICAL METHODS IN ENGINEERING, 15, 1, 43-56, English, 1069-8299, WOS:000078409500005 - A comparison between the volumetrically elastic and deviatorically rigid-plastic FEM and the penalty rigid-plastic FEM
YM Guo; Y Yokouchi; K Nakanishi; S Kamitani
The volumetrically elastic and deviatorically rigid-plastic finite element method (FEM) is a different method from the conventional penalty rigid-plastic FEM, and has some merits in comparison with the penalty rigid-plastic FEM. To secure numerical evidence on the difference between the two kinds of methods and to show the merits of the volumetrically elastic and deviatorically rigid-plastic FEM, this paper makes analyses of the upsetting of an aluminium alloy column by the two kinds of methods. Then, normal solutions are compared with deviant solutions that are given by relaxing convergence criteria of the iterative solution in a calculated step by the two kinds of methods, respectively. In this way, it can be clarified that the errors of the step virtually disappear, and that the calculated results are largely corrected in the next step and the later steps for the volumetrically elastic and deviatorically rigid-plastic finite element analysis. Copyright (C) 1999 John Wiley & Sons, Ltd., JOHN WILEY & SONS LTD, Jan. 1999, COMMUNICATIONS IN NUMERICAL METHODS IN ENGINEERING, 15, 1, 43-56, English, 1069-8299, WOS:000078409500005 - 剛塑性有限要素法の収束生
Sep. 1998, 第61回塑性力学分科会, 1-6 - 非線形有限要素法
Dec. 1994, コロナ社 - 体積弾性・偏差剛塑性有限要素法
Aug. 1994, 日本塑性加工学会、塑性と加工, 35, 403, 965-970 - Adaptive load incrementation algorithm during a process of local unloading in the elastic-plastic finite element analysis.
YOKOUCHI Yasuto; NAKAMURA Motoichi
There are two approaches in the incremental finite element analysis of elastic-plastic problems; one takes an explicit scheme using forward Euler integration formula with adaptive load incrementation, the so-called rmin method, and another implicit scheme with iterative procedures such as the Newton method. This paper discusses an algorithm of determining incremental step size in the former approach. A new additional restriction is proposed for the determination of the loading factor rmin when unloading takes place. A concept of admissible error is introduced where errors in stress increments are defined as the difference between one computed by assuming the elastic-plastic constitutive relation and the other computed by assuming the elastic relation. The error norm should be restricted within specified value. Numerical examples are demonstrated to show that the algorithm is reasonable., The Japan Society of Mechanical Engineers, Dec. 1990, Transactions of the Japan Society of Mechanical Engineers Series B, 56, 532, 2437-2442, Japanese, 0387-5008, 110002373265, AN0018742X